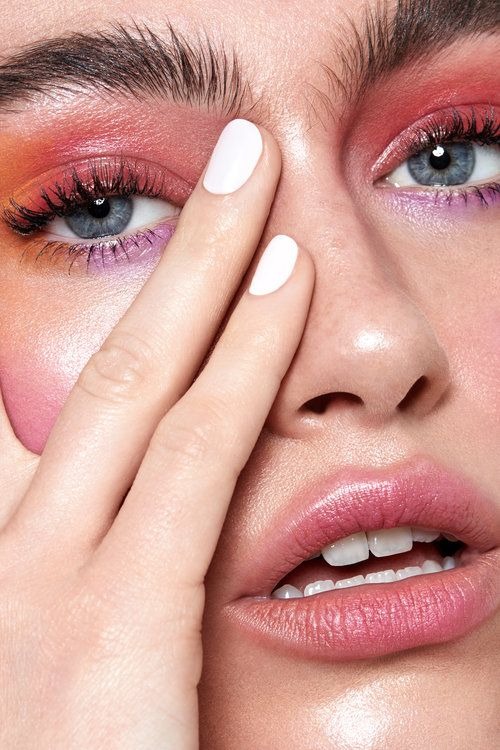
Can Your Porcelain Veneers Keep Up with Sydney’s Coffee Obsession?
Picture this: you’re rushing through Martin Place, triple-shot flat white in hand, when you catch your reflection in a shop window. Your smile? Still flawless, even after three coffees before lunch. But wait—can those pearly whites handle Sydney’s caffeine addiction without turning into a dental disaster? Let’s chat about how modern teeth veneers hold up against our city’s love affair with coffee.